Levels of Automation Continue to Increase
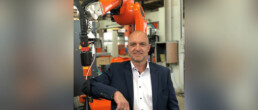
“We’re very pleased that it’s finally possible to hold on-site trade fairs again. Personal exchange with customers, potential customers and partners at trade fairs will continue to play an important role in the future.” Stephan Pittner, CTO at Carl Cloos Schweißtechnik GmbH, has announced that live link-ups to the manufacturing facilities in Haiger will be set up during Blechexpo/Schweisstec 2021. Trade fair visitors will thus be able to gather information directly concerning solutions for automated welding and get answers to their questions from the experts on site.
Which current topics and trends is the sheet metal working industry currently dealing with?
The degree of automation will continue to increase in both upstream and downstream processes. More and more frequently, our customers want to integrate solutions for automated welding technology with different manufacturing technologies into the production line, for example grinding applications. In addition to this, advancing digitalisation facilitates optimal control and continuous improvement of robotic welding systems. Artificial intelligence is also becoming increasingly significant and will be an important partner to humans in the factory of the future. This is why we’re constantly expanding our range of digital solutions.
How do you see the positioning of German sheet metal working and welding technology companies with regard to digitalisation and automation?
Industry 4.0 strives to depict the production of an individual product from initial order to final delivery. We support our customers in this regard. The point is to manufacture individualised solutions in a fully automated manner – we supply all systems with a robot as a central component to this end … from a single source. Today we’re capable of simulating all of the processes of the robotic system with the help of a digital twin. To an ever greater extent, the welding power source and the robot are evolving into a system that can optimise itself. In addition to acquiring all production data such as welding parameters, arcing times, program runtimes and various efficiency indicators, it’s particularly important for users to have this data available quickly in a clear format. Platform-based online tools are becoming increasingly prevalent in this regard. Users are able to access information from their welding production processes in real time with our C-Gate IoT platform. We’re currently working on the ability to incorporate simpler upstream and downstream processes, which are already being used by beta testers.
The transformation of the automotive industry has begun – which challenges and opportunities will this present to the sheet metal working industry?
We implement integrated manufacturing solutions for a wide range of industry sectors. Thanks to our broad-based positioning, we’re not affected by changing conditions in the automotive sector to the same extent as other companies. But the shift to e-mobility will present us with a number of opportunities. For example, demand for battery systems will continue to grow. We can make use of our manufacturing expertise for the production of these components.
How important is it for you personally, and for your company, to demonstrate presence at trade fairs and to exchange ideas with customers in person – in particular at Blechexpo/Schweisstec 2021?
We’re very pleased that it’s finally possible to hold on-site trade fairs again. Personal exchange with customers, potential customers and partners at trade fairs will continue to play an important role in the future. Digital formats are a tremendous enhancement, but they can’t entirely replace face-to-face interaction.
Which product highlight will you showcase at Blechexpo/Schweisstec 2021 in Stuttgart?
Visitors will be able to experience the steadily expanding product range of QINEO welding equipment at live demonstrations in the manual welding area. With its outstanding price-performance ratio, the QINEO StarT provides a great new entry-level solution for the world of modern MIG welding technology. The QINEO NexT high-tech welding power source offers excellent welding results and flexible application options in manual and automated welding. The QINEO QuesT will soon supplement the portfolio for high-end TIG applications as a new benchmark. Beyond this we’ve further developed our QIROX robot portfolio, our robot control and digital products such as our C-Gate IoT digitalisation platform, and our QIROX RoboPlan offline programming software. We’ll also establish live link-ups to our manufacturing facilities in Haiger from our trade fair booth. Our visitors will thus be able to gather information directly concerning our complex solutions for automated welding and get answers to their questions from the experts on site.